Posted by Zosi Team
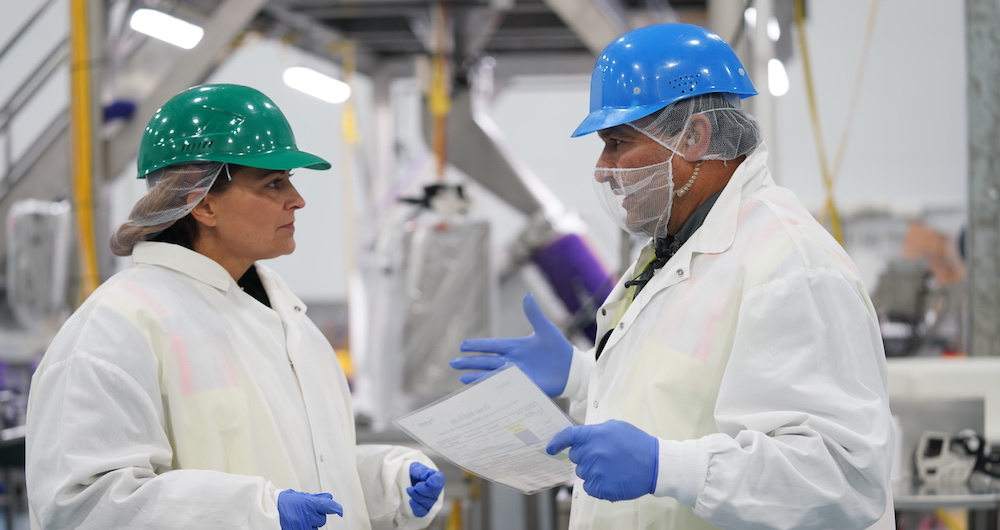
Continuous quality improvement is more of a philosophy than a process or system. It requires commitment from everyone in the business. Everyone from senior management to frontline workers must adopt a mindset of continuously looking for ways to improve processes and systems by making them efficient and effective. Unsustainable continuous improvement efforts are those that fail to become part of a company’s culture.
Attributes & Benefits of Successful Continuous Improvement
Continuous quality improvement relies heavily on the following attributes to ensure success in the intended scope and purpose of the application:
Continuous improvement success doesn’t just result in company longevity. In addition, companies that emphasize such strategies reap benefits like market leadership, exceeding customer expectations, improved product quality, increased productivity and participation during training, improved operational capabilities, and more.
Six Sigma
While lean manufacturing is used primarily in production, another common methodology used outside of manufacturing is the Six Sigma method. While Six Sigma and Lean Manufacturing share a common goal, the former focuses on eliminating variation in the final product. Six Sigma implements process improvements by using DMAIC methodology as a means of root cause analysis. DMAIC stands for define, measure, analysis, improvement, and control.
Define – Define a problem or improvement opportunity and how it is affecting your current production.
Measure – Measure current process performance. This includes identifying what isn’t working in order to find new ways of continuous improvement.
Analyze – Analyze the process to determine the root causes of the problem. Can the process be improved? Should it be reconfigured altogether?
Improve – Address root causes by employing and testing new solutions
Control – Continue to make improvements over time. Ensure that employees have developed a culture of improvement so that they are able to refine and maintain successful processes that meet any demand for organizational change.
Conclusion
Organizations must consider continuous improvement a normal part of the operation, rather than a siloed program. Continuous quality improvement fails when:
Continuous improvement processes, like Six Sigma, provides workforces with more effective ways accomplish their everyday tasks. Whichever process you choose, there is an opportunity to employ HACCP principles, root cause analysis procedures, and CAPA processes. In food manufacturing, the success of your continuous improvement strategy will rest on your ability to seamlessly integrate these principles into practice.